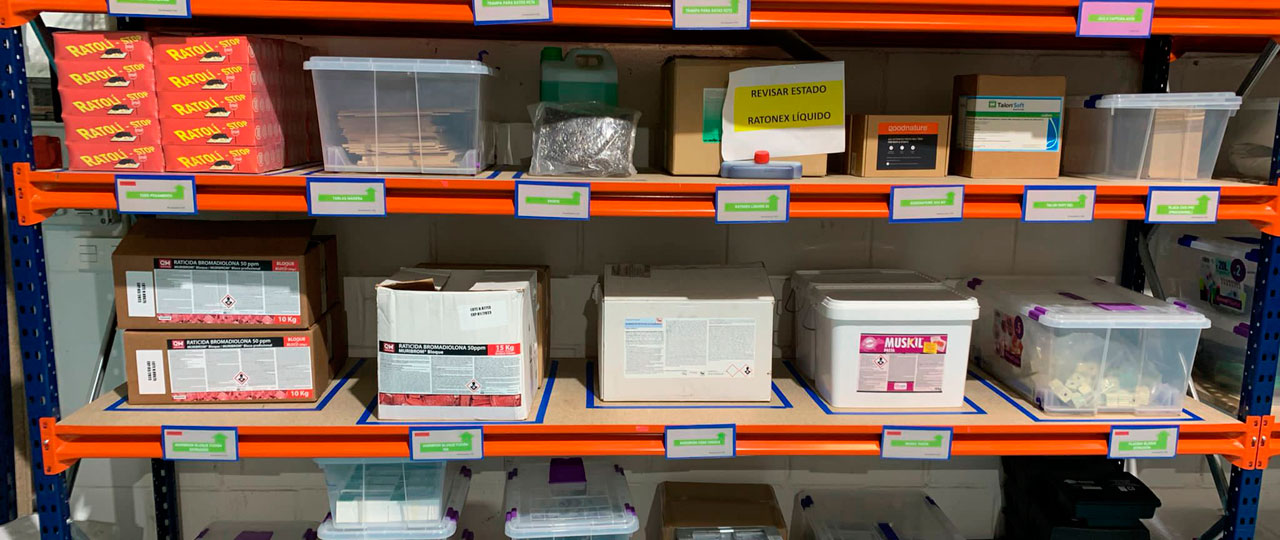
Experiencia de implantación real de las 5S en Insec Sanidad Ambiental
Hoy queremos compartir con vosotros la experiencia de transformación vivida en la empresa INSEC Sanidad Ambiental (podéis conocerles un poquito a través de su web www.insec.es y sus redes sociales).
Insec es una pyme con la que tenemos el placer de trabajar desde hace casi 8 años. Es una típica pyme vasca, volcada en su buen hacer en el cliente. Inquieta por mejorar continuamente. Estábamos en un punto, en el que algo había que hacer para dar un nuevo impulso a la gestión, a la motivación del equipo, a la organización del trabajo, a facilitar el día a día, a mejorar las condiciones de trabajo…. lo teníamos difícil, el nivel era altísimo cuando le propusimos al gerente de Insec la implantación de una herramienta japonesa denominada las 5S.
Si queréis averiguar lo que son las 5S, teclearlo en Google. Wikipedia lo explica perfectamente y entidades como Euskalit aportan valor al respecto. Sin embargo, aquí os queremos resumir lo que han supuesto las 5S en Insec.
A Unai, gerente de Insec, disciplinado hasta la médula, practicante de Karate desde hace más de 25 años, solo hubo que frenarle en su entusiasmo al ver lo que podían proporcionarles las 5S. De buenas a primeras quería implantarlo en el 100% de las instalaciones y de golpe. Si algo nos enseña la metodología es a ir paso a paso, sin atajos, sin prisas. Así que le convencimos de que eligiera un área piloto significativa y seleccionara el equipo responsable de la implantación en dicho área.
Eligió el almacén de materiales y herramienta. El lugar, estaba ordenado y limpio, pero tal y como se ve en las fotos, y en el resultado final, el punto de partida era mejorable. Implantar las 5S, no es simplemente organizar y limpiar. Consiste en una transformación de la cultura de la empresa, implica cambiar el chip totalmente y hacer partícipe de ese cambio a todo el personal y a otras personas que pueden incidir en el día a día de la empresa (pe: transportistas, proveedores…).
Para cambiar la cultura, hay que empezar por transformar el pensamiento, la forma de ver y de procesar la información de lo que vemos. Hay que analizar y procesar muchísima información. Y empezamos por transformar a un equipo de 4 personas multidisciplinares. A estas 4 personas, de diferentes áreas y rangos las formamos en la metodología 5S y les “obligamos” a aplicar sus nuevos conocimientos en el área piloto. El proceso de formación incluye una breve sesión teórica y pasa a la acción inmediatamente. Dicen que si lo aprendido no se pone en marcha en un corto periodo de tiempo se pierde…
La primera S (Seiri) implica decidir qué es lo necesario o innecesario en el lugar o para la actividad que se desarrolla en dicho lugar. Y no veáis lo que cuesta decidirlo. Por este motivo empezamos a definir criterios que faciliten la toma de decisiones. Por ejemplo: si no está en perfecto estado de uso es un innecesario que se elimina….aquí hay que inventariar los elementos existentes y después las decisiones que se adoptan al respecto, materializando dichas decisiones.
Por ejemplo, bajamos al área piloto y en medio de la estantería encontramos una botella de agua medio vacía. Primero lo documentamos (por escrito y mediante foto) y segundo decidimos que se hace con ella. No se trata de retirarla a la basura sin más. Porque si no se analiza lo sucedido y no se establecen medidas para evitarlo, siempre pueden volver a aparecer botellas de agua semillenas donde no deben. Y la botella simplemente es un ejemplo de todo lo innecesario que podemos almacenar donde no se debe.
Una vez hemos decidido que es necesario e innecesario, nos quedamos con lo necesario y pasamos a aplicar la segunda S (Seiton). En esta S, se ordenan los necesarios. A la hora de ordenar, hay que tener en cuenta la seguridad, el uso, el tamaño…. de los elementos (herramientas, materiales…). En este punto hay que volver a establecer criterios que faciliten el trabajo, generando un entorno más seguro si cabe.
Una vez que está todo ordenado, toca aplicar la tercera S (Seiso) que es Limpiar. Aquí hay una premisa única a tener en cuenta que “no es más limpio quien más limpia, si no quien menos ensucia”. La limpieza, pasa a ser responsabilidad de todo el personal, y es aquí donde el responsable del almacén dio un salto de alegría porque estaba cansado de ser el “único” en limpiar y andar detrás del resto del equipo para que colaboren. Aquí se planifican las tareas de, frecuencias y responsables de la limpieza, y lo que es casi tan importante, se establecen mecanismos para facilitarlas y reducir los tiempos dedicados a estas tareas tan poco productivas.
Una vez implantadas las tres primeras Ss, descorchamos la botella de cava para celebrarlo. Es un hito y en sí, conlleva una mejora considerable.
Tras la celebración, pasamos a la cuarta S (Seiketsu). En esta S, nosotros tenemos nuestra propia metodología y la consideramos como la S del control visual y la estandarización. Tocaba darle al coco, pensando en las mejores soluciones para estandarizar los contenedores, facilitar el control visual, facilitar la gestión de las herramientas de trabajo compartidas, de los EPIs….y tras darle de lo lindo al coco (pe: se estandarizan colores y etiquetados…), y de implantar las medidas, estábamos ante otro almacén, ante otro pabellón (hasta se pintó el suelo con una pintura especial en un color diferente, azul…).
Pero lo mejor no era lo evidente, un almacén espectacular, práctico, visualmente atractivo, limpísimo y sencillo de usar (a la altura del pensamiento japonés Poko yoke), había cambiado la forma de pensar y percibir el entorno de trabajo del equipo 5S, y estos a su vez habían cambiado al resto de personas que componen Insec. Ya nadie quería volver al punto de partida y querían aplicar los nuevos conocimientos en más áreas. Por ejemplo, administración se puso a eliminar carpetas AZ innecesarias, saliendo cerca de una tonelada de papel innecesario a destruir…antes les faltaban estanterías y ahora les sobran.
En esta cuarta ese habíamos transformado la cultura de Insec. Ahora la clave estaba en cuidar los detalles, y por eso seguimos trabajando a diario la quinta S (Shitsuke), la más complicada porque la rueda de la Mejora Continua no debe detenerse nunca…en este compromiso se realizan periódicamente las auditorías 5S donde ya no pasaría desapercibida una botella de agua fuera de su lugar, porque ahora hay un nombre para cada “cosa” y cada “cosa” está con su nombre en su ubicación correspondiente.
Espero que la experiencia de Insec os ayude y motive a seguir mejorando, porque las 5S es un método que ayuda, y no seremos nosotros quienes os hablen de sus ventajas. Animaros a implantarlas y si es con nuestra ayuda, mejor.
Iker Fernandez Artigas
Gerente de Ifkonsulting